File Management Solution
Step 1
RFID tags are attached to items such as products, pallets, or containers, enabling them to be tracked throughout the warehouse.
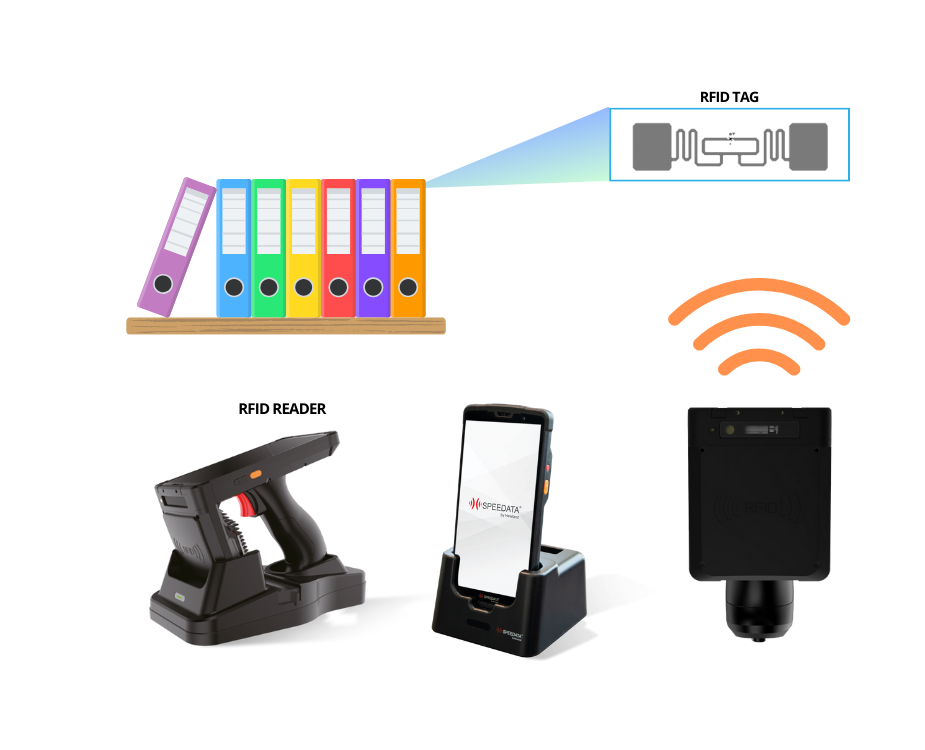
How File Management Solution Works
Physical documents or assets are equipped with RFID tags containing unique identifiers, enabling automated tracking and identification across various locations or facilities.
RFID readers positioned strategically throughout designated areas emit radio waves to detect RFID tags, capturing tag IDs and their locations in real time.
Upon detecting RFID tags, readers transmit tag IDs to a central database instantly, updating the database with current asset locations and status.
The system automates inventory management by continuously monitoring and recording asset movements, ensuring accurate inventory counts, and reducing manual tracking errors.
Detailed audit trails and compliance reports track asset movements, ensuring adherence to regulatory requirements such as chain of custody for sensitive documents.
The system offers endless features, including:
Provides continuous, real-time visibility of assets or documents equipped with RFID tags.
Generates visual maps or floor plans showing the real-time location of assets within facilities.
RFID readers automatically detect and identify tagged items as they move through reader zones.
Defines virtual boundaries to trigger alerts when assets move in or out of specified areas.
Tracks and manages inventory levels, reducing stockouts and overstock situations.
Manages assets from acquisition through to disposal or retirement, optimizing asset use.
Ensures only authorized personnel have access to specific assets based on RFID tag permissions.
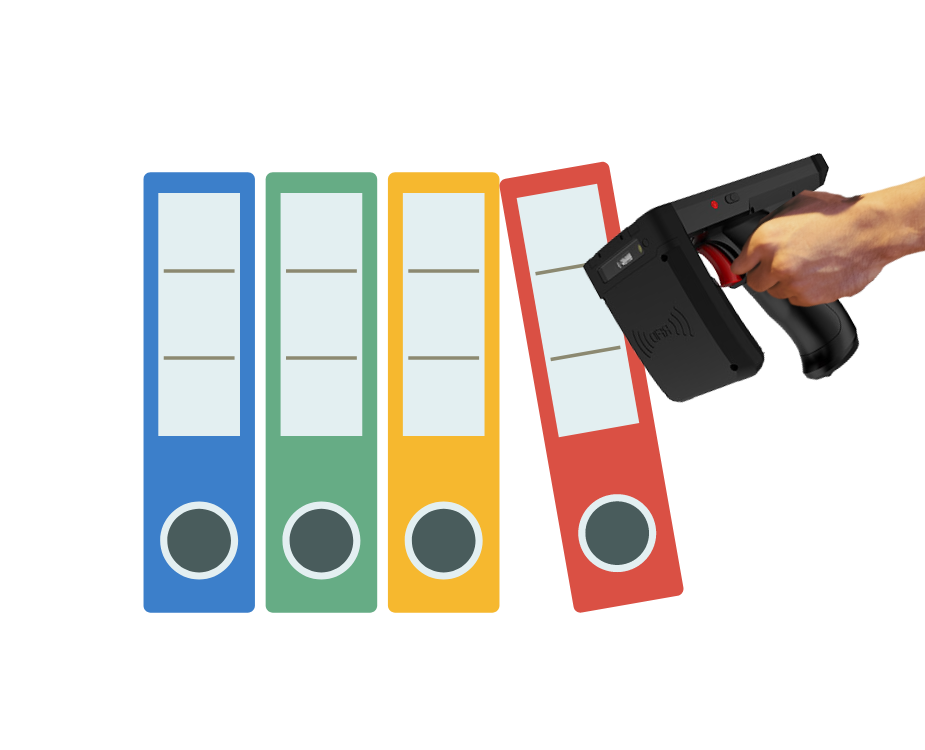
Three Key Components for Effortless Advancement
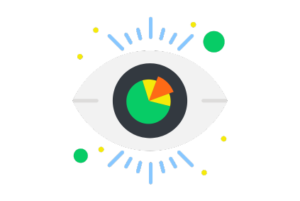
Enhanced Asset Visibility
RFID technology enables real-time tracking and monitoring of physical assets or documents, providing precise location data at any given time. This visibility minimizes the time spent searching for misplaced items, improving operational efficiency.
Improved Inventory Accuracy
Automatic tracking and inventory updates reduce manual errors associated with traditional inventory management methods. Accurate inventory data enables better resource allocation and reduces stock discrepancies.
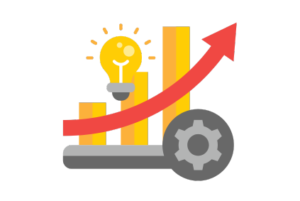
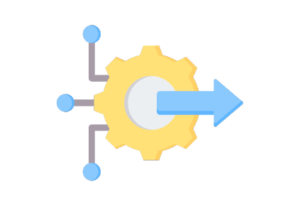
Streamlined Operations
Automated check-in/check-out processes and workflow integration optimize asset management processes. This streamlining reduces administrative burden and enhances overall operational efficiency.
It takes 3 step to automate the problems

Step 1

Step 2
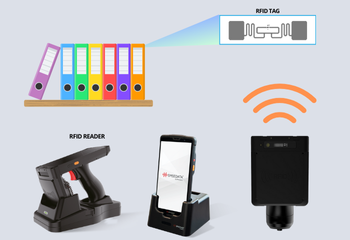
Step 3
Case Studies

Retail Shop
Increase inventory accuracy, boost process efficiencies and reduce out-of-stocks with item-level tagging. Poxo(Poxo RFID Automation) for retailers can provide full inventory visibility from warehouse to individual retail outlets. In addition, stock taking which typically require a few days can be done within minutes with mobile RFID devices.

Warehouse
Improve efficiency and accuracy throughout your entire warehouse operation with RFID Fixed Gantry for automated inventory update. Streamline receiving, put-away, picking and shipping operations with greatly simplified tracking process by taking only a fraction of the time it would otherwise have taken to count and monitor the items manually with Poxo(Poxo RFID Automation).
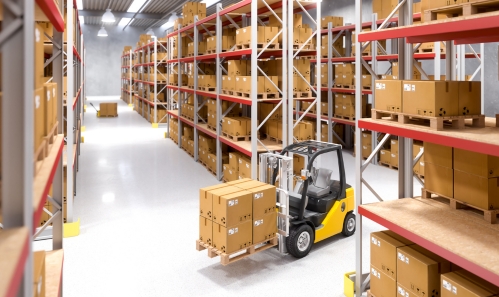
Racking & Forklifts
Automatically verifying pallet identification and rack/door location to avoid mis-shipments or erroneous placements, Poxo(Poxo RFID Automation) for forklift’s customization can provide pinpoint load location, assign dynamic routing, monitor load time, reduce empty moves, and improve the overall productivity and utilization of your forklift fleet.